What Matters Most in the Design of EV HV Wiring Harness?
The high-voltage wire harness can be divided into motor HV wiring harness, battery high voltage wires, and fast charging high voltage wires etc. It mainly provides high-voltage power supply for new energy vehicles. The design of the wiring harness is therefore critical to ensure that it can withstand the high voltages and currents that are encountered in the vehicle. Its design mainly involves the working voltage, working temperature, temperature rise, wire diameter, cable protection and the selection of high voltage connectors.
The rated power of electric motors used in electric commercial vehicles is relatively large -- generally between 50 and 150 kW. It can reach more than 200kW on some electric heavy trucks. To minimize the energy loss during high voltage electric power transmission and to reduce the impact of the current on the electrical system, it is necessary to properly increase the operating voltage of the EV power system. The working voltage of high-voltage components of electric commercial vehicles is generally at 540~600 V DC, and the highest voltage can reach about 750 V DC. Therefore, the operating voltage of the high voltage wiring harness is generally selected at 1000 V DC or 1500 V DC.
Working temperature: it refers to the highest temperature at which it can operate without damage during its normal service life under normal conditions of use. A wire harness can be damaged if it operates outside its rated temperature range because it will generate heat due to its resistance when current flows through it.
Temperature rise: it is how much hotter a wire gets after being subjected to high currents over long durations. If you're using a particular material for your vehicle's wiring harness that has a low working temperature but a high temperature rise (such as aluminum), you might want to consider using some additional heat shielding on any components where there will be a lot of heat generated by large currents.
At present, the ambient temperature is generally -40℃ ~ +85℃. The long-term maximum allowable working temperature on the surface of the high-voltage wire harness is 125℃, which can reach to 150℃ in some special applications.
When designing EV HV wiring harness, it is required that the operating temperature ≥ ambient temperature + temperature rise. When using high-voltage wire harnesses, it is generally required that the temperature rise not exceed 55K.
At 125℃, see Table 1 for the matching of the cross-sectional area of copper core cables and the current carrying capacity.
Table 1
The bending radius of the high-voltage wire harness has a great influence on its resistance. The smaller the radius of the cable, the greater the resistance to deformation and rupture. If the high-voltage cable is excessively bent, the resistance of the bent part becomes larger, which will cause a large voltage drop on the line.
Taking Guchen HV Cable for example, when the outer diameter of the cable is large than 20mm, the bending radius should not be less than 6 times the outer diameter. If it is too small, there may be mechanical damage caused by repeated bending due to vibration or other factors during operation.
A high voltage connector should have excellent electrical performance and mechanical strength which can withstand shock loading and vibration during operation of an electric vehicle without failure due to fatigue or corrosion over time. They also provide weather protection for high voltage wires in outdoor environments where there is exposure to rain, snow or other harsh weather conditions.
◆ Protection class ≥ IP67
◆ The connectors should be constructed to provide IPXXB level of touch safety, protection from direct contacts.
◆ Insulation resistance ≥ 500MΩ, 1000V DC
◆ The operating voltage of HV connectors should no less than that of the electric vehicle.
◆ Mechanical fool-proof function
◆ High-voltage interlock function
◆ Secondary locking function, to avoid the risk of high-voltage electric shock due to misoperation or bumps during use.
◆ The connector must have a shielding ring to meet the crimping requirements for high-voltage shielded cables.
A variety of high voltage connectors are available on the market nowadays, so choosing a suitable one can help reduce costs while ensuring reliability during operation. Commonly used connectors include pass-through connector, metal connector, and plastic HVIL connector.
Terminals crimped onto the wires should be strong enough to withstand the high voltage load without deforming or breaking off from the wire during installation or use. Crimping also helps ensure that all connections in the harness are properly secured and conductive enough for efficient current flow.
Table 2
The shielding layer may also be made of aluminum foil. It can effectively reduce the impact of electromagnetic interference caused by the high voltage cable itself (such as corona discharge and arc discharge). Aluminum foil has good electrical conductivity and heat dissipation capacity, which makes it safer and more reliable than other materials in terms of insulation resistance. It also has excellent resistance to electric shock because it is able to conduct electricity away from the human body quickly when touched on a live line.
Related Reading:
The Role of Shielding Design of High Voltage Wiring Harness for Electric Vehicles
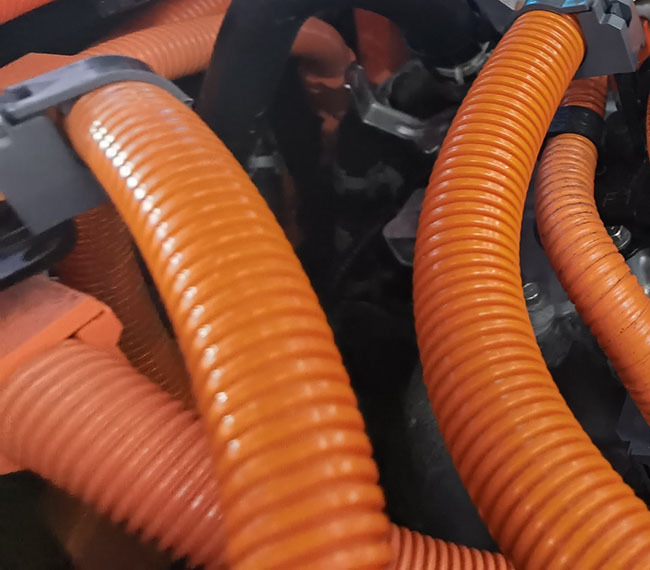
Corrugated Tubes
Table 3
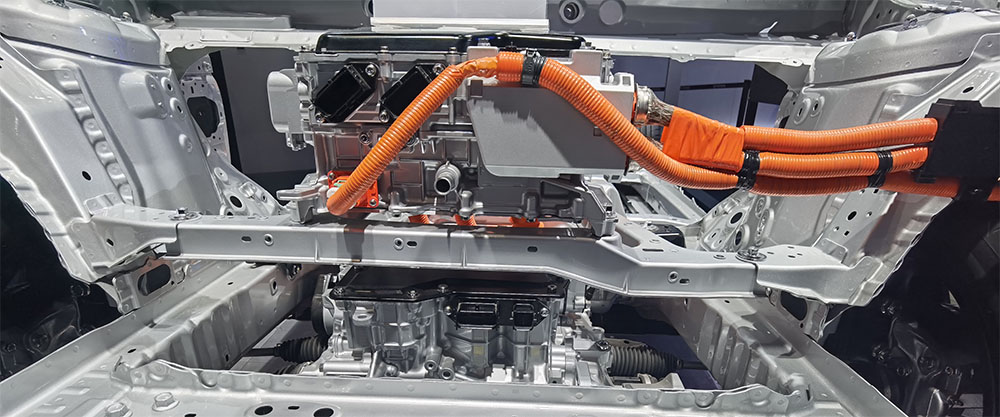
Operating Voltage
The working voltage of an EV wire harness refers to the maximum voltage that can be safely applied to the wires in a specific wire harness.The rated power of electric motors used in electric commercial vehicles is relatively large -- generally between 50 and 150 kW. It can reach more than 200kW on some electric heavy trucks. To minimize the energy loss during high voltage electric power transmission and to reduce the impact of the current on the electrical system, it is necessary to properly increase the operating voltage of the EV power system. The working voltage of high-voltage components of electric commercial vehicles is generally at 540~600 V DC, and the highest voltage can reach about 750 V DC. Therefore, the operating voltage of the high voltage wiring harness is generally selected at 1000 V DC or 1500 V DC.
Working Temperature & Temperature Rise
The working temperature and temperature rise are two important factors to consider when designing an EV HV wiring harness.Working temperature: it refers to the highest temperature at which it can operate without damage during its normal service life under normal conditions of use. A wire harness can be damaged if it operates outside its rated temperature range because it will generate heat due to its resistance when current flows through it.
Temperature rise: it is how much hotter a wire gets after being subjected to high currents over long durations. If you're using a particular material for your vehicle's wiring harness that has a low working temperature but a high temperature rise (such as aluminum), you might want to consider using some additional heat shielding on any components where there will be a lot of heat generated by large currents.
At present, the ambient temperature is generally -40℃ ~ +85℃. The long-term maximum allowable working temperature on the surface of the high-voltage wire harness is 125℃, which can reach to 150℃ in some special applications.
When designing EV HV wiring harness, it is required that the operating temperature ≥ ambient temperature + temperature rise. When using high-voltage wire harnesses, it is generally required that the temperature rise not exceed 55K.
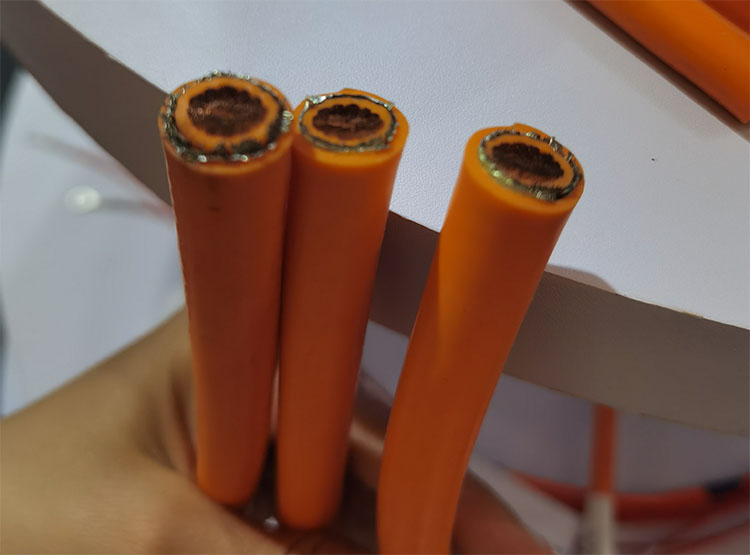
Wire Diameter
The diameter of the wire determines the current carrying capacity of the cable. The greater the diameter, the higher the current carrying capacity. Large wires have lower resistance than smaller ones, so they are able to handle more current without overheating or catching fire due to excessive current flow. They also have better thermal characteristics, which means they can dissipate more heat when carrying heavy loads or working at high temperatures.At 125℃, see Table 1 for the matching of the cross-sectional area of copper core cables and the current carrying capacity.
Cable Cross-sectional Area (mm2) | Safe Current Carrying Capacity (A) |
6 | 50 |
10 | 70 |
16 | 100 |
25 | 125 |
35 | 150 |
50 | 200 |
70 | 250 |
95 | 280 |
120 | 320 |
Bending Radius
Wire bending radius is the minimum radius that the wire can be bent without causing permanent deformation. It should be large enough so that when the cable is bent, it does not damage the insulation layer or conductor.The bending radius of the high-voltage wire harness has a great influence on its resistance. The smaller the radius of the cable, the greater the resistance to deformation and rupture. If the high-voltage cable is excessively bent, the resistance of the bent part becomes larger, which will cause a large voltage drop on the line.
Taking Guchen HV Cable for example, when the outer diameter of the cable is large than 20mm, the bending radius should not be less than 6 times the outer diameter. If it is too small, there may be mechanical damage caused by repeated bending due to vibration or other factors during operation.
High Voltage Connector Selection
High voltage connectors are used to connect EV cable to other high voltage components such as motor control unit and power distribution unit. They are of paramount importance in the design of HV wiring harnesses.A high voltage connector should have excellent electrical performance and mechanical strength which can withstand shock loading and vibration during operation of an electric vehicle without failure due to fatigue or corrosion over time. They also provide weather protection for high voltage wires in outdoor environments where there is exposure to rain, snow or other harsh weather conditions.
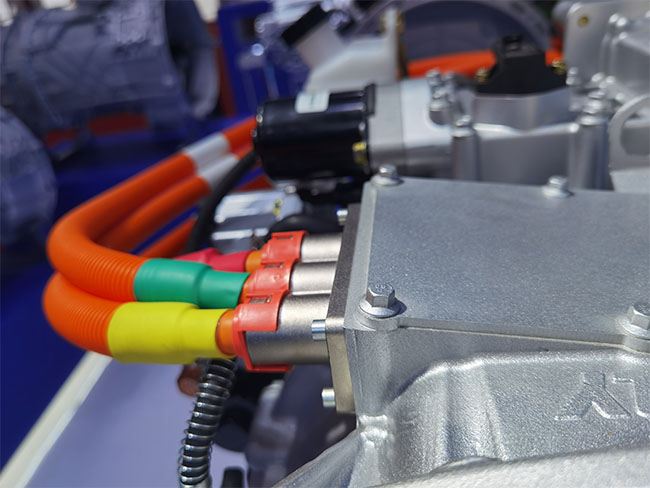
◆ The connectors should be constructed to provide IPXXB level of touch safety, protection from direct contacts.
◆ Insulation resistance ≥ 500MΩ, 1000V DC
◆ The operating voltage of HV connectors should no less than that of the electric vehicle.
◆ Mechanical fool-proof function
◆ High-voltage interlock function
◆ Secondary locking function, to avoid the risk of high-voltage electric shock due to misoperation or bumps during use.
◆ The connector must have a shielding ring to meet the crimping requirements for high-voltage shielded cables.
A variety of high voltage connectors are available on the market nowadays, so choosing a suitable one can help reduce costs while ensuring reliability during operation. Commonly used connectors include pass-through connector, metal connector, and plastic HVIL connector.
Terminals Crimping
Electrical terminals crimping is an important step in EV HV wiring harness design since it ensures that critical electrical connections are secure and reliable throughout their lifetime by forming an electrical connection between two conductors (known as terminals).Terminals crimped onto the wires should be strong enough to withstand the high voltage load without deforming or breaking off from the wire during installation or use. Crimping also helps ensure that all connections in the harness are properly secured and conductive enough for efficient current flow.
![]() |
![]() |
![]() |
Terminal Profile Analyzer | Terminal Pull Tester | Terminal Voltage Drop Tester |
Analyzing the distribution and crimping of wires on the terminal crimping end face | Test to verify terminal crimping | Used to detect contact performance impedance after terminal crimping |
Shielding Layer
Shielding layer can protect the circuit and cable from electromagnetic interference, which can reduce the impact of electromagnetic interference on the performance of electronic devices. It plays an important role in protecting the signal inside the cable from external interference. In some cases, this can be achieved with a copper wire mesh or spiral shielding.The shielding layer may also be made of aluminum foil. It can effectively reduce the impact of electromagnetic interference caused by the high voltage cable itself (such as corona discharge and arc discharge). Aluminum foil has good electrical conductivity and heat dissipation capacity, which makes it safer and more reliable than other materials in terms of insulation resistance. It also has excellent resistance to electric shock because it is able to conduct electricity away from the human body quickly when touched on a live line.
The Role of Shielding Design of High Voltage Wiring Harness for Electric Vehicles
High Voltage Cable Protection
After the crimping process is completed, the outer surface of the high-voltage wire harness should be wrapped with orange corrugated tubes, braided tubes or textile tapes to increase its wear resistance, insulation and aesthetics.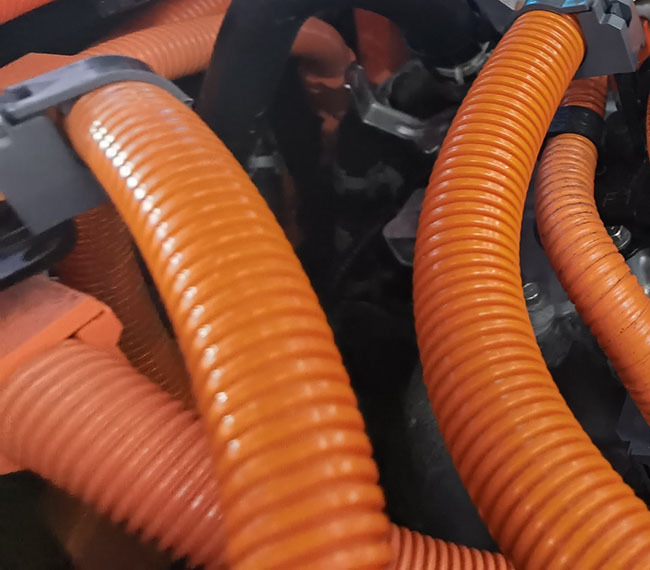
Corrugated Tubes
Outer surface materials | Wear-resistant | Reduce crush damage | Waterproof and dustproof | Thermal insulation | Cost | Size |
Closed Corrugated Tubes | Yes | Yes | Yes | No | Low | Large |
Open Corrugated Tubes | Yes | No | No | No | Low | Small |
Braided Tube | Yes | Yes | No | No | High | Small |
Braided Tape | Yes | No | No | No | High | Small |
PVC Tape | Yes | No | Yes | No | Low | Small |
Insulation Resistance Detection
This test checks the resistance between conductors in a cable assembly or between conductors and ground or neutral. If the insulation resistance is too low, it may indicate that the cable assembly has been damaged or has been subject to moisture or other contaminants that could cause insulation breakdowns or failures. The insulation resistance must not be less than 500MΩ at any point of the cable.----------------------------------------------
The importance of a quality EV HV Wiring Harness cannot be overstated. The failure of a single wire in the high-voltage (HV) system can result in severe damage to property and even personal injury. This is why it is so important to choose a manufacturer that has experience making high-quality, durable and reliable HV wiring harnesses for the EV industry.
Message
If you are interested in our products, please fill in the message form below. Our sales representative will contact you within 24 hours.