The Future Development Trends of Global EV Technology
1. Battery Technology: Higher Energy Density, Higher Level of Safety
The higher the energy density of the battery, the more power it can store per unit volume.In the past 20 years, the global automotive industry has carried out in-depth research on the following directions of EV batteries:
1) How to efficiently and safely store electrical energy in the battery and drive the vehicle system to operate efficiently and intelligently
2) How to improve the energy density of power batteries and greatly increase the cycle life, including the development of new high-nickel cathode materials, silicon-carbon composite anode materials, and new electrolytes, etc., so as to overcome battery energy storage technology and make batteries with higher energy density, lower costs, and longer life;
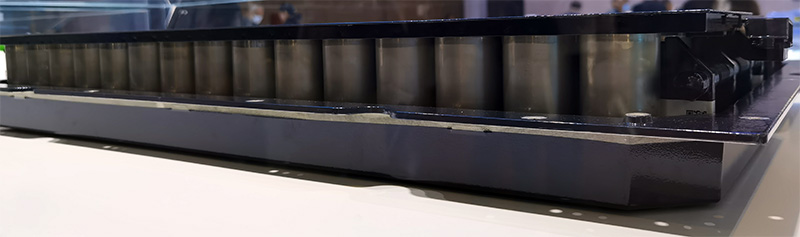
Technology representative in TWh Era: In September 2022, in conjunction with solid-state and high energy density technologies, Farasis Energy released the Super Pouch Solution (SPS). SPS is a large soft package iteration platform, no module integration:
◆ Integration reaches 75%, and components are reduced by 50%
◆ Compatible with ternary, iron-lithium, sodium batteries, graphite, silicon carbon, lithium metal and other material systems. The energy density is from 270 to 400Wh/kg, which can meet the battery life of 300-1000 kilometers
◆ 400 kilometers of battery life after 10 minutes of charging, using AI management throughout the life cycle to ensure safe operation.
At the same time, TWh's technology and production line will greatly reduce production capacity investment costs and manufacturing process costs, reducing equipment investment by 50%, reducing plant area by 60%, and products reaching the PPb level, achieving zero-carbon manufacturing and carbon neutral standards.
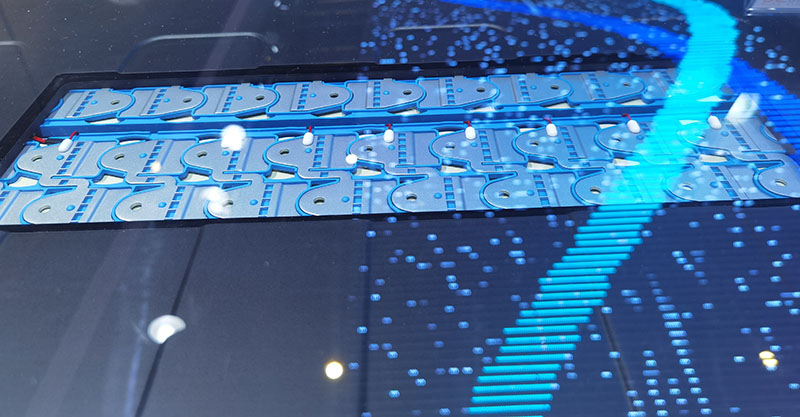
The first step is to reach the limit of energy density of existing lithium batteries, which is 350wh/kg;
The second step is to realize the transformation of battery form, from liquid to semi-liquid and finally to solid-state batteries.
The third step is to achieve the industrialization of solid-state batteries with an energy density of 500wh/kg by 2035.
2. Super Fast Charging Technology
Fast charging is the enabler and accelerator for the popularization of electric vehicles. According to a research report by McKinsey, the fast and convenient charging has replaced the purchase cost and mileage anxiety, and become the NO. 1 problem hindering the widespread popularization of EVs. From the perspective of social cost, the construction of fast charging technology & network is imperative.The problems faced by high-power charging: First, the construction cost is high. Second, due to the higher charging power, the fast charging pile itself will have higher load requirements on the grid, which is an intractable problem for the construction of high-power charging stations. It requires the charging station builders and operators to fully consider the load capacity of the local power grid, and to fully negotiate with the local power grid company to reach a cooperation, and the power grid expansion is a big project.
Overcome charging technology to make charging faster, smarter, and more versatile: In response to the range anxiety, many EV manufacturers have launched a technology competition in the past two years. Electric car with 600km range has become the mainstream of the market. Models with 800km-1000km range are also launched. At the China EV100 Forum 2023 held in early April, Li Bin, chairman of Nio Inc., announced that the installation of 500kW ultra-fast charging piles has begun; XPeng G9, launched in September 2022, is China's first mass-produced vehicle based on an 800V high-voltage SiC platform. In addition to China's EV companies developing ultra-fast charging technology, the same is true for international auto giants such as Porsche, Tesla, and BMW. Tesla announced that as of early March 2023, it has deployed more than 1,500 high-power charging stations and more than 10,000 high-power charging piles in mainland China, as well as more than 700 destination charging stations and 1,900 destination charging piles, and formed a "15-minute charging" life circle in Beijing, Shanghai, Shenzhen and other cities.
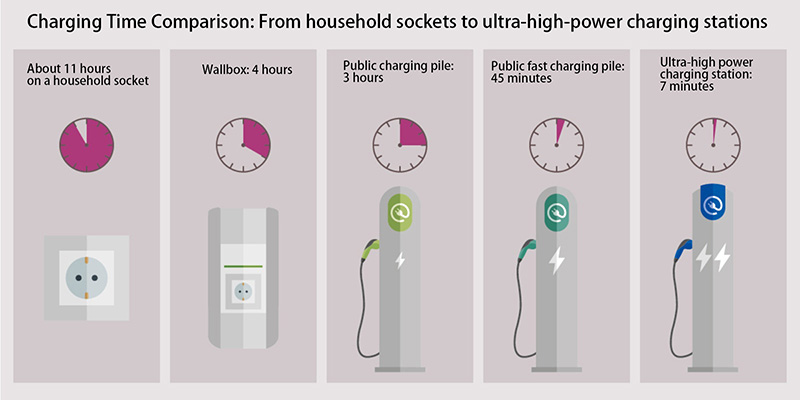
Upgrading the high-voltage platform has two main advantages:
First, it can break through the limitation of high current and achieve higher charging power. Continuing to increase the charging current will pose a huge challenge to the heat dissipation of the electric vehicle charging cable. While upgrading the voltage platform to a higher level will open up room for further improvement of the charging power;
Second, 800V platform can improve the efficiency of the electric vehicle system operation and increase cruising range. Under the same operating power, increasing the voltage platform can reduce the current passing through HV electrical equipment such as high-voltage wiring harnesses and electric motors, thereby reducing copper loss and improving operating efficiency. At user end, the energy consumption level is greatly optimized, and the battery life is longer and more reliable.
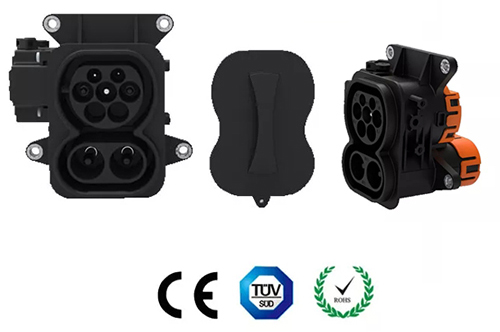
3. More Innovative Cable Connections and Wire Harness Solutions
The electrical system of battery electric vehicles is complex, and requires more wires and cable harnesses to transmit electric energy. For example, the battery management system requires high-quality wiring harness to connect a large number of sensors to monitor battery power, voltage, temperature and other parameters. At the same time, fast charging and high power output also requires high-voltage wiring harness to provide power supply to vehicles. The main characteristics of EV cables include high voltage, high current, large wire diameter, and a large number of wires, which have a high technical threshold. This determines that EV HV cable faces challenges such as safety, wiring, shielding, weight and cost.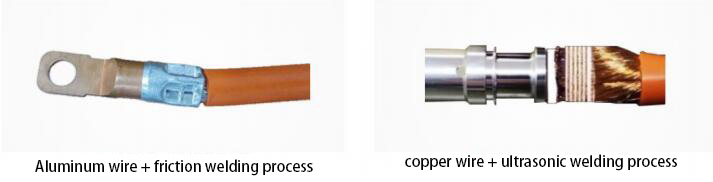
In addition, the EV market pays more and more attention to the weight reduction and energy saving of vehicles. The wire harness processing industry also needs to follow this trend, and constantly explore new materials and processes to reduce the weight and energy consumption of wire harnesses. The use of new high-conductivity materials, lightweight skin and structural design can reduce the weight of the wiring harness itself, thereby improving the vehicle performance.
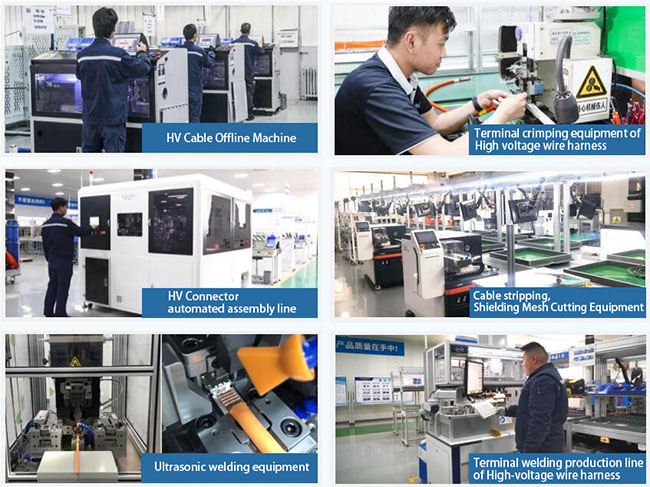
Technology representative: Guchen Electronic has launched impressive products and technologies, including
1) high-voltage interlock connectors that are compact, rich in options, and can support copper/aluminum conductor welding/crimping solutions,
2) and charging sockets with high precision and simple assembly.
In terms of "customization", Guchen Electronic can quickly customize and develop reliable EV connection solutions according to customer needs by virtue of years of intensive cultivation. All developed products will pass rigorous tests to meet the quality requirements of the automotive industry.
In terms of "cost performance", Shenzhen Guchen Electronic relies on scale advantages, complete upstream and downstream supply chains, information integration, strong production capacity, and efficiency advantages of advanced intelligent manufacturing, to provide global customers with super cost-effective EV interconnection solutions.
4. Industrial Robot
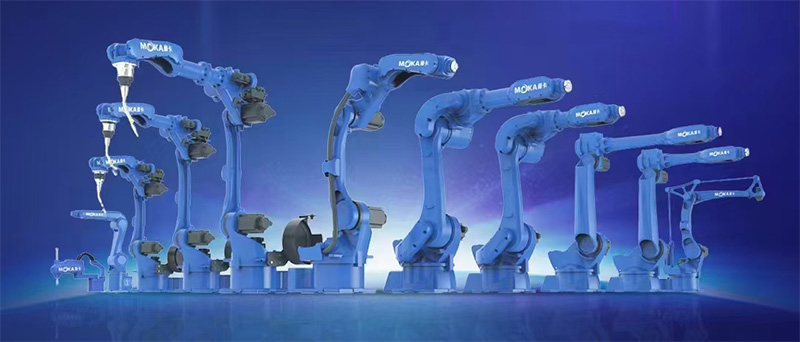
In fact, FANUC's new energy vehicle manufacturing solutions are widely used in BYD, Li Auto, XPeng, AION, AITO and other customers. FANUC has gathered a wealth of experience in the intelligent manufacturing of battery electric vehicles, power batteries, and powertrain systems to help users develop smart manufacturing.
5. New Adhesive Dispensing and Fluid Filling Technology
In automobile production, including the manufacture of battery packs, electronic control boards and other components, due to the large output, robots are basically used for automatic dispensing. Although the automatic dispensing process has high efficiency, its cost and technical difficulty are also very high. It is necessary to ensure that the glue is evenly applied on the surface of the parts to be connected, and to control the amount of each injection, so that the connection between the parts is firm and uniform, so as to improve the safety and reliability of the battery pack.
With the rapid development of the global EV industry, it has created many new issues. It is necessary for the upper and lower industrial chains to advance with each other's “connection force”, focus, gather strength, and cooperate sincerely to jointly promote the further development of the global electric vehicle industry, including how to meet the needs of large-scale production, meet consumers' pursuit of high performance, meet the market's cost control and so on.
Message
If you are interested in our products, please fill in the message form below. Our sales representative will contact you within 24 hours.