The High Voltage Design in Battery Electric Vehicles
1. High Voltage Warning Sign
High-voltage warning signs are used to warn car owners not to touch them for safety reasons. Battery electric vehicles usually use two forms of high-voltage warning signs, including high-voltage marks/labels and high-voltage warning colors.High voltage mark and label are installed on high-voltage components, with clear indication that they are not safe for people to touch. After-sales service personnel can intuitively see the possible dangers of high voltage through the mark. The marks used are based on the international standard of hazard sign warning of dangerous electrical voltage.
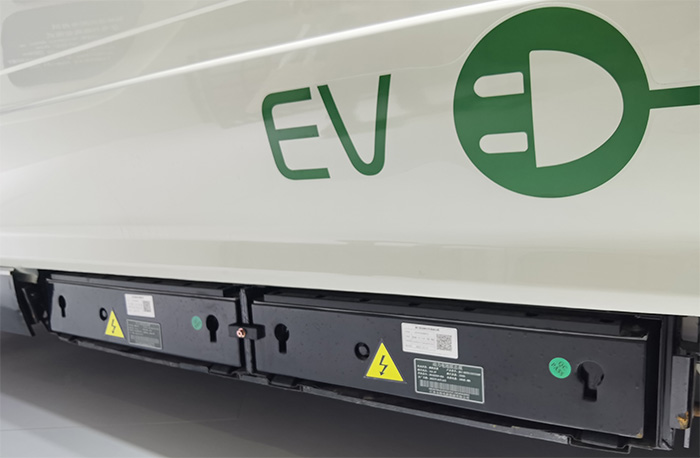
Orange is the color of danger and caution, a bright and easily recognizable color that can be seen from a distance. This makes it ideal for safety purposes as workers can spot any potential hazards before they get too close to them or become injured by them. It is used for traffic signs to warn motorists of hazards or dangerous conditions ahead. Orange also represents the color of fire, which relates to electrical shock hazards associated with high voltage electrical equipment.
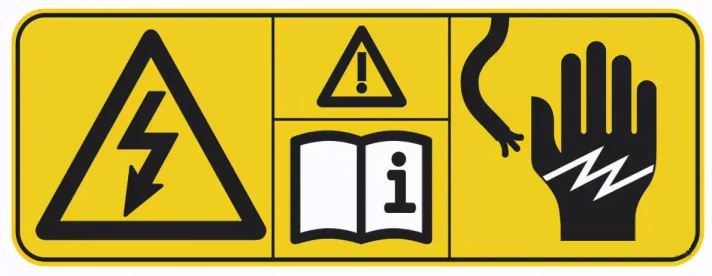
The use of high-voltage warning signs and colors can effectively prevent accidental contact with high-voltage systems by maintenance personnel or car owners during maintenance work or after service.
2. High Voltage Safety Design for New Energy Vehicles
In our previous article, we know that potential safety hazards of new energy vehicles include high-voltage system short circuit, high-voltage system insulation failure, high-voltage system disconnection, high-voltage charging risk, etc. According to these potential safety hazards and actual driving conditions, the safety design of electric vehicles is mainly from the following aspects, as shown in the figure: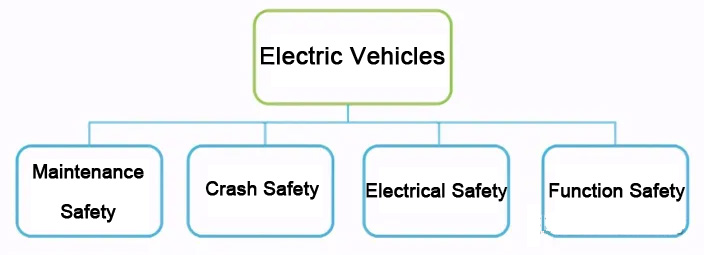
2.1 Maintenance Safety
Maintenance safety of hybrid and electric vehicles is mainly to prevent high voltage electric shock. Most electric cars are designed with a manual service disconnect (MSD) on the system, which can be easily operated by hand to isolate the battery from the power supply. The MSD is placed in the following positions: 1) The outer box of the battery pack; 2) Integrated in the high-voltage box (PDU). If multiple battery packs are involved in a commercial vehicle, multiple MSDs may be used.When performing major overhaul, maintenance, or replacement of high voltage components, it is necessary to turn off the MSD switch to ensure the safety of both personnel and vehicle.
Tips: Disconnect the power transmission of EV’s battery pack. Wait for another 5 minutes before proceeding further or touching HV parts.
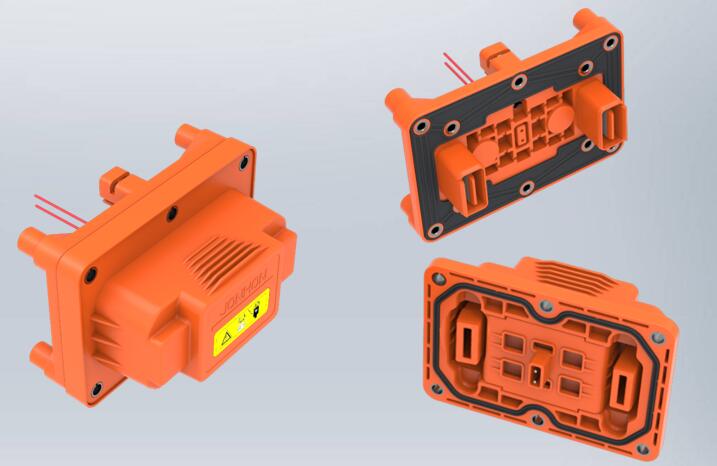
2.2 EV Crash Safety
When an electric vehicle collides, the vehicle should protect the passengers from damage to the extent possible during and after the collision.In order to achieve this goal, the EV safety system must meet the following requirements:
The structure of the vehicle must be strong enough to withstand external impacts and distribute forces evenly throughout its body. If a collision occurs at high speed, it is preferable that there is no deformation or damage to the passenger compartment. The impact absorption mechanism must react quickly enough to ensure that passengers do not suffer from whiplash injuries or other serious injuries due to excessive acceleration or deceleration. The strength and stiffness of all components should be sufficient so that they can withstand collisions with other vehicles or objects without suffering any significant damage.
◆ The battery pack must be protected against fire, explosion and other hazards caused by high-speed collisions.
◆ During and after collision, there should be no electrical hazards caused by short circuits or static electricity discharge on sensitive components such as touch screens and displays; this refers mainly to power supply lines between high voltage components in electric vehicles.
For this reason, some EVs are designed with a circuit as shown in the figure:
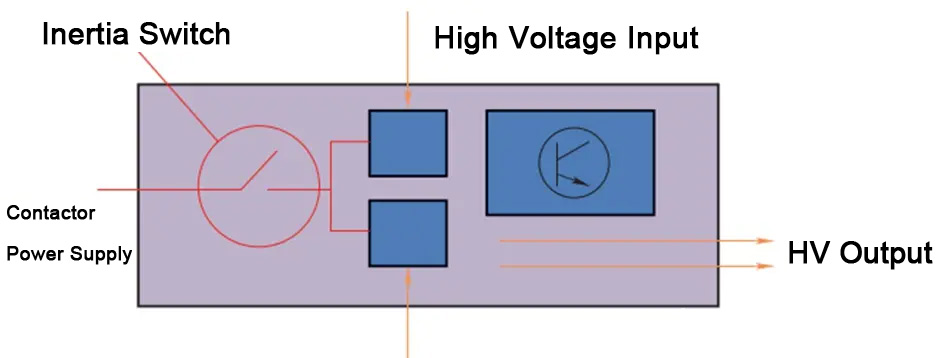
2.3 Electrical Safety
In order to ensure the electrical safety of battery electric vehicles, some EVs are designed with the following safety devices:◆ Water-proof and anti-dust high voltage connectors
The high voltage connector is a waterproof connector for interconnection of high voltage battery and other EV components. They should be withstand water pressure from any direction without leakage. The high voltage connector is also dustproof so that it does not get damaged by dust during transportation or storage. In addition, this type of connector can pass through all kinds of tests, such as vibration test, heat test and so on.
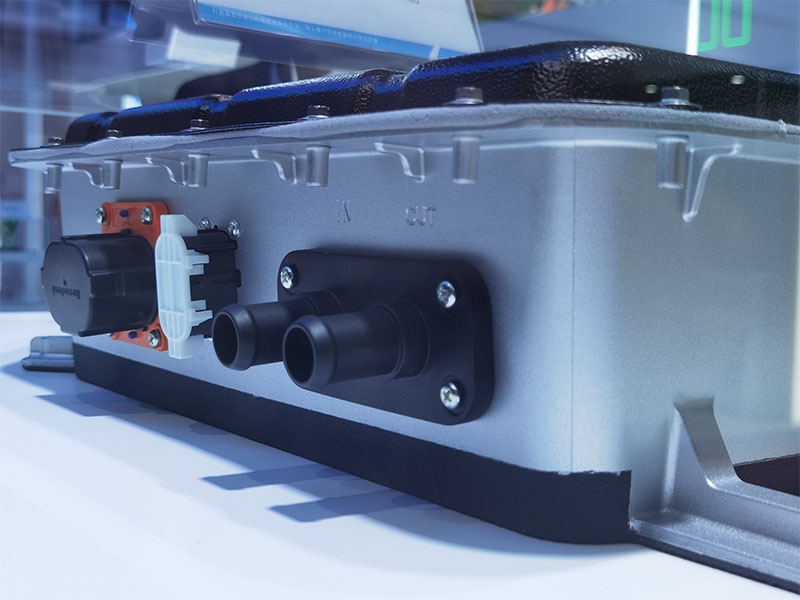
The contactor can be opened at any time, and is controlled by an automatic control device. When it is opened, it will stop charging or discharging, ensuring that there is no danger of electric shock when charging or discharging.
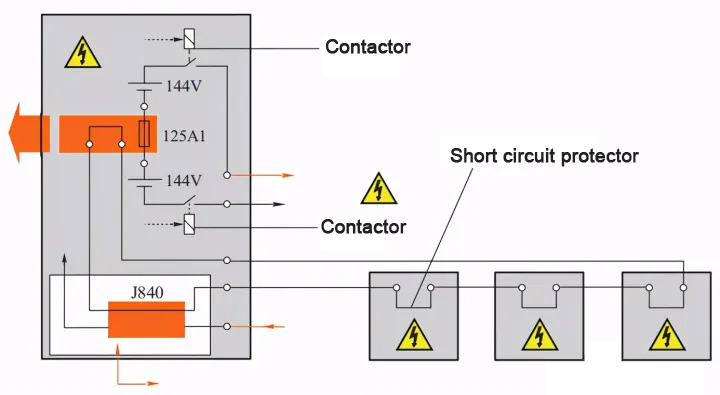
The pre-charging circuit prevents the charger from applying current to a vehicle that has not been fully discharged. It mainly consists of precharge resistor. The resistor limits current flow until the battery reaches a high enough voltage level to allow current to pass through the compensation capacitance.
PS: compensation capacitor is designed between the positive and negative poles of the high-voltage components
◆ Insulation resistance detection system
This system monitors the insulation degree of the automotive high voltage cable relative to the vehicle chassis, by dividing the voltage between the positive power cable & chassis, and the negative power cable & chassis. To simplify the structure, the insulation resistance monitoring module is usually set in the power battery system, and the insulation resistance monitoring function is integrated into the BMS.
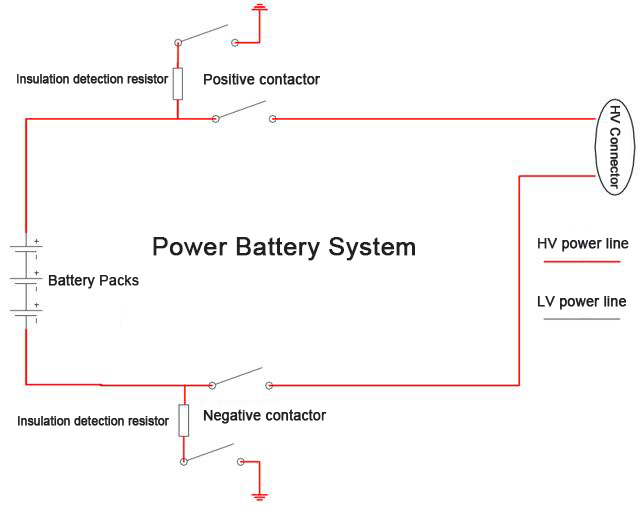
◆ Short circuit protector
It is used to protect against an accidental short circuit in the high voltage system. A short circuit occurs when a path from one pole of a battery to another is accidentally created by physical contact or by a broken wire. When such a path is created, excessive current flows through it and can cause damage to the battery and its components. The short circuit protector detects this condition and shuts down or limits current flow until the problem has been corrected.
◆ High voltage interlock loop design
The high-voltage interlock design can monitor the continuity of the high-voltage circuit, and send an alarm signal to the VCU before the high-voltage power failure, so that the VCU can take countermeasures for the entire vehicle system.
Another risk existing in electric vehicles is human misoperation during system operation and manual disconnection of high voltage automotive connectors. The high-voltage interlock design can disconnect the output of the power battery at the same time when the connector is disconnected to avoid electric shock.
2.4 Function Safety
◆ Torque Safety ManagementIn order to prevent the unexpected movement of the vehicle, it is necessary to add a torque safety control strategy in the VCU. The specific strategy is as follows:
① The VCU is responsible for calculating the torque demand. If the difference between the calculated torque demand is greater than a certain calibration value, it is considered that there is a safety risk in the torque output. At this time, the VCU will limit the vehicle speed to a safe range.
② If the difference between the required torque of the VCU and the actual torque of the motor is greater than a certain calibration value, it is considered that the torque control of the motor is at risk, and the VCU will limit the torque output of the electric motor. If the difference between the two is always too large, the power transmission of the power battery will be cut off.
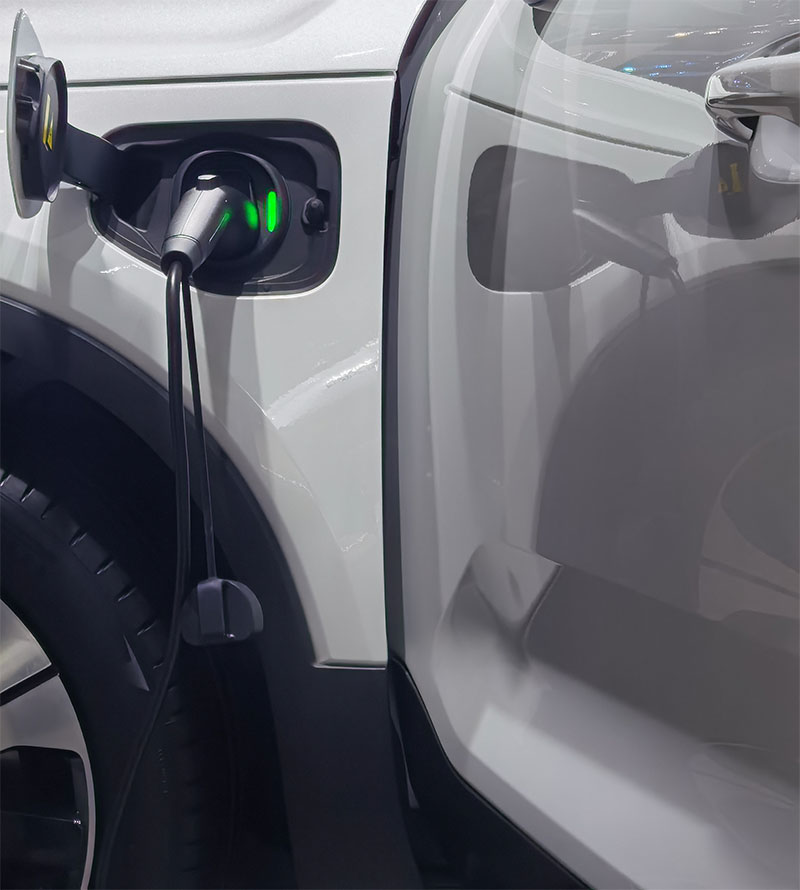
When charging, it is necessary to prevent the vehicle from moving, and avoid conflicts between fast charging, slow charging, and driving modes. For this purpose, the following designs are made:
① Charging is allowed only when the gear is in the P position.
② During the charging process, both the torque demand and the actual torque output should be 0.
③ When the EV charging cable is plugged in, it is not allowed to close the contactor that controls the high voltage output.
④ When the insulation resistance of the charging circuit is lower than the resistance value required by the standard, the charging should be stopped and the high-voltage contactor should be disconnected.
Message
If you are interested in our products, please fill in the message form below. Our sales representative will contact you within 24 hours.