Optimization of Shielding Structure in EV High-Voltage Cables
1.Design Concept
Traditional vehicles typically have a warranty period of 3 to 5 years. Their wiring systems mainly operate under low voltage and low current conditions, so the cable structures are simple—mostly consisting of a conductor and insulation. Due to the small cable size, low voltage/current transmission, and minimal electromagnetic interference (EMI), shielding was generally unnecessary.However, with the rapid development of new energy vehicles (NEVs), the automotive industry is becoming increasingly intelligent and automated. Many design oversights have emerged, such as the mismatch between cable lifespan and the overall vehicle service life. In the past, traditional vehicles were heavily mechanical with limited electronics, making EMI concerns negligible. As a result, shielding was rarely considered in automotive cable design.
Today, the growing complexity of automotive electronics means signal acquisition, transmission, and reception are highly susceptible to both internal and external electromagnetic interference, which can lead to signal distortion or even safety incidents. Therefore, modern automotive electronic components require proper EMI protection to both block external interference and prevent emitted electromagnetic waves from affecting nearby components.
Three-phase motors are now commonly used in NEVs. The sinusoidal voltage signals they transmit—akin to square-wave pulses of varying frequencies—produce high-frequency harmonics due to their steep wavefronts, which can cause significant EMI to surrounding electronics. Although HV cables in NEVs do not transmit data like coaxial cables and therefore do not require shielding for data integrity, they must be shielded to suppress electromagnetic radiation generated during current transmission. This is essential for preventing interference with adjacent components and ensuring the stable operation of nearby electronics.
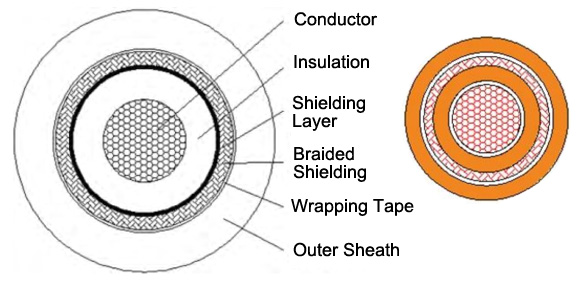
To address this issue, a new cable design has been introduced where a tinned copper braided shield is layered over an extruded semi-conductive shielding layer (see Cross Section in Figure 1). In this design, the Al/PET tape is replaced with an extruded semi-conductive layer, ensuring consistent lifespan across all cable components while maintaining excellent shielding performance. This fully satisfies the service life requirements of NEV components.
2. Analysis of High Voltage Shielding Cable Structures
2.1 Copper Braided Shield Only
Using only copper wire braiding offers longer lifespan, unaffected by the limitations of Al/PET tape. However, braided shields are inherently porous due to their cross-weave structure, leaving diamond-shaped gaps (see Figure 2). These gaps reduce the coverage area and thus compromise the shielding effectiveness. The shape and area of these gaps vary based on braiding parameters, which in turn directly affect transfer impedance. As EMI requirements become more stringent with vehicle electrification, copper braiding alone can no longer meet performance standards and is now largely obsolete.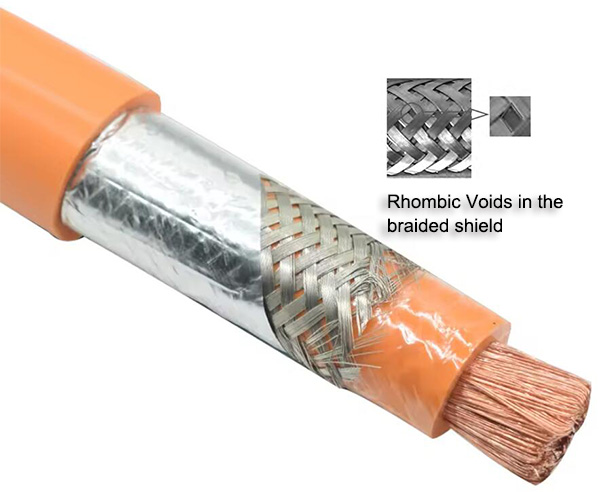
2.2 Copper Tape Shielding
Wrapping copper tape around cables provides excellent shielding and durability. However, this design makes the cable stiff with a large bending radius, making it unsuitable for installation in the confined spaces of modern vehicles. As such, it fails to meet basic automotive design criteria and is not considered viable.2.3 Al/PET Tape + Copper Braid Composite Shielding
Currently, the standard shielding structure for in-vehicle HV cables consists of Al/PET tape wrapping combined with copper wire braiding. This offers excellent shielding effectiveness and flexibility for tight-space routing, meeting OEM and industry standards. However, tests simulating harsh vehicle environments—such as high humidity or exposure to acidic, alkaline, or salty conditions—have shown that the aluminum layer in the tape degrades quickly, becoming brittle and breaking, which leads to a rapid decline in shielding performance and increased risk.2.4 Extruded Semi-Conductive Layer + Copper Braid Shielding
Leveraging years of experience in high-voltage power cable manufacturing, it is found that the shielding techniques used in power transmission cables can be applied to NEV HV cables. The extruded semi-conductive layer has a proven long service life, even over decades, with no significant performance degradation.With mature triple-layer co-extrusion technology, a modified dual-layer co-extrusion method can simultaneously extrude the insulation and the semi-conductive shielding layer. This prevents delamination, air pockets, or foreign material intrusion between layers, thereby avoiding swelling or other quality issues under heat. The semi-conductive layer’s thickness can be maintained around 0.3 mm, which does not significantly affect overall cable diameter or weight—meeting OEM demands for lightweight and compact components.
Prototype testing confirms that this new structure (extruded semi-conductive shield + tinned copper braid) meets both shielding and longevity requirements. Furthermore, this method eliminates an additional process step, improves concentricity, and enhances overall product quality and softness. Compared to Al/PET tape wrapping, this method improves both production efficiency and cost-effectiveness. Repeated production and testing have validated that this new structure can fully replace the traditional Al/PET + braid composite, solving the cable lifespan limitations caused by Al/PET degradation.
3. Cable Shielding Performance
National standard GB/T 25087-2010 and automotive industry standard QC/T 1037-2016 both define shielding effectiveness requirements for HV cables, including transfer impedance and shielding attenuation tests, with the transfer impedance measured using the triaxial method being most commonly used.As shown in Table 1, test results confirm that the shielding performance of the redesigned cable is not compromised, verifying the effectiveness and feasibility of the new design.
Cable Structure | Test Frequency (Hz) | Test Result (mΩ·m⁻¹) |
Wrapped Al/PET Tape + Braided Composite Shield | 0–500 | 15.96 |
Extruded Semi-conductive Layer + Braided Composite Shield | 0–500 | 13.68 |
Table 1 Comparison of Transfer Impedance Test Results for Two Cable Structures
4. Cable Flexibility Testing
NEVs face challenges of limited interior space. Existing platforms were originally designed for gasoline engine components and must now accommodate additional electronic components, making efficient space utilization essential. Limited routing space and tight bend radii call for flexible cables that are easier to install during vehicle assembly, improving manufacturing efficiency and throughput.The dual-layer co-extrusion method described in this paper avoids additional process steps, maintains good concentricity, reduces final cable diameter, and enhances product quality. Compared to traditional Al/PET wrapped cables, the extruded design provides significantly better flexibility and user-friendliness. This solution meets both productivity and quality control requirements.
Table 2 compares the cold bend performance of the two cable structures.
Cable Structure | Test Conditions | Test Result |
Wrapped Al/PET Tape + Braided Composite Shield | Stored at −40 °C for 8 h, then wound 1.2 turns around a mandrel with diameter 5D in a low-temperature chamber | No cracking in any cable layer |
Extruded Semi-conductive Layer + Braided Composite Shield | Same as above | No cracking in any cable layer |
Table 2 Comparison of Cold Bend Test Results for Two Cable Structures
5. Cable Service Life Testing
The traditional HV cable structure in NEVs is:Conductor + Insulation + Al/PET Tape + Copper Braid + Sheath.
Among these, the Al/PET tape has the shortest service life due to its material characteristics. Even under mild conditions, it may not last the minimum 3-year warranty period of vehicles. In extreme environments (humidity, acids, alkalis, salt fog), its lifespan may be less than 3 months.
The redesigned cable aims to align the service life of all structural components, ensuring that the cable's warranty meets or exceeds that of traditional vehicles. Table 3 compares long-term damp heat aging tests between the two shielding methods.
Results show that Al/PET deteriorates rapidly in harsh environments, becoming brittle and prone to breakage under bending or external force, rendering the shielding ineffective and reducing the cable’s total lifespan.
In contrast, the extruded semi-conductive layer has a lifespan consistent with that of the entire cable. In the absence of mechanical damage or external impact, it can reliably function for 5 to 10 years, satisfying NEV service life requirements.
Message
If you are interested in our products, please fill in the message form below. Our sales representative will contact you within 24 hours.