4 Ways to Prevent Automotive High-Voltage Wiring Harness Failures
High-voltage wiring harnesses are essential to the safe and efficient operation of electric vehicles. These harnesses reduce installation time, optimize space, and shield electrical circuits from shocks, vibrations, debris, and other environmental hazards. In automotive applications, HV harnesses power critical systems such as traction motors, onboard chargers, battery management systems, and power distribution units.
However, a failure in the HV harness can compromise both the safety and performance of the entire vehicle. A loose or damaged HV cable can result in open or short circuits, and faults in the HVIL can disable safety-critical components. In worst-case scenarios, overheating or electrical arcing may lead to fires. Understanding the causes of HV harness failures—and how to prevent them—is essential for automotive engineers, OEMs, and harness manufacturers. Here are four key areas to focus on:
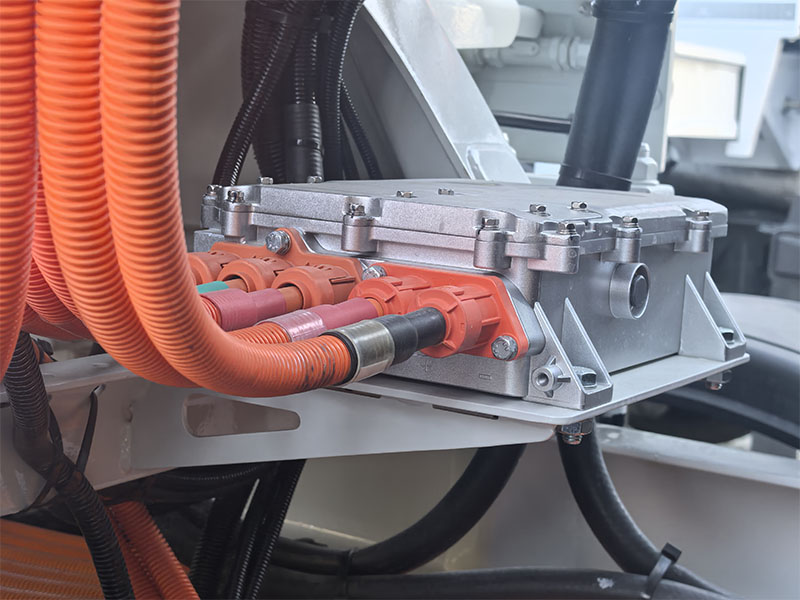
Work with experienced suppliers who use precision cutting and crimping equipment, adhere to strict quality standards, and understand the specific power and safety requirements of EV platforms. Simulation tools and 3D harness routing should also be employed to verify fitment, reduce EMI risks, and prevent mechanical interference.
Modern EV platforms also demand shielding against EMI to avoid cross-talk between control signals and high-voltage lines. Mismatched shielding or grounding paths can degrade signal integrity and system reliability. Ensure compatibility between all mating parts and pay attention to interface standards such as IP67/IP6K9K ratings, dielectric strength, and mechanical keying.
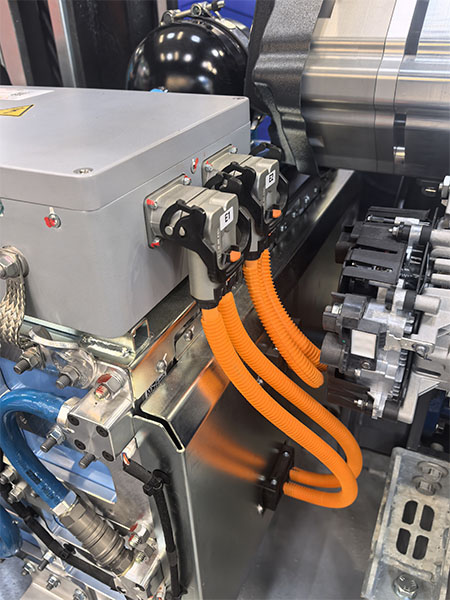
Instead, use automotive-grade, finely stranded copper conductors and XLPE or silicone-based insulation materials with excellent thermal and dielectric properties. Similarly, overmolded seals and grommets must maintain flexibility and integrity in extreme conditions to prevent water ingress, insulation breakdown, or connector corrosion.
Automated crimp force monitoring, pull tests, and cross-sectional analysis should be standard quality checks. When soldering is required (especially for sensor wires or braided shields), technicians must follow precise thermal profiles to avoid cold joints or insulation damage. In EVs subject to vibration and thermal cycling, poor joints can become hot spots or trigger HVIL faults.
Work with trained personnel, calibrated tools, and documented assembly processes to maintain consistency and reduce variability.
Final Thoughts
Preventing high-voltage harness failures in electric vehicles requires a comprehensive approach—from robust design and material selection to proper assembly and testing. By collaborating with experienced harness manufacturers and specifying components tailored to EV environments, OEMs can ensure that their high-voltage systems deliver safe, reliable, and long-lasting performance.
However, a failure in the HV harness can compromise both the safety and performance of the entire vehicle. A loose or damaged HV cable can result in open or short circuits, and faults in the HVIL can disable safety-critical components. In worst-case scenarios, overheating or electrical arcing may lead to fires. Understanding the causes of HV harness failures—and how to prevent them—is essential for automotive engineers, OEMs, and harness manufacturers. Here are four key areas to focus on:
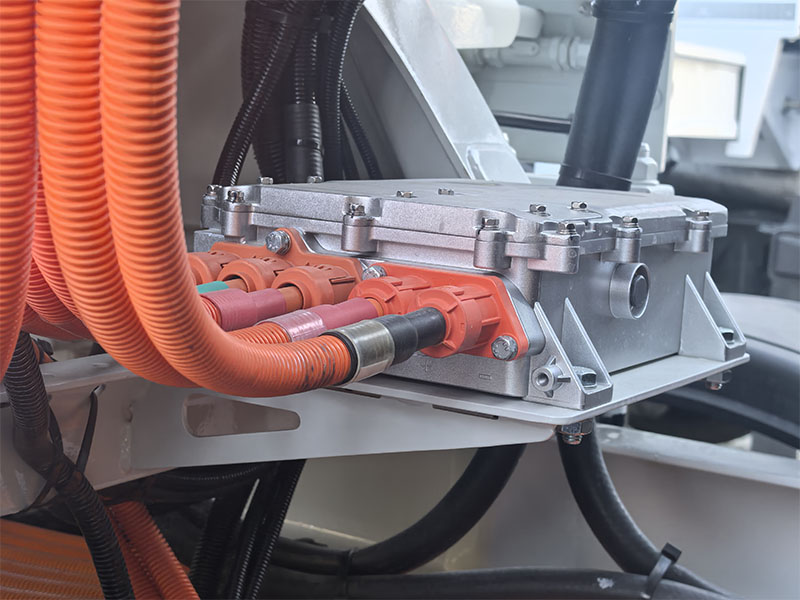
1. Prioritize Robust and Application-Specific Design
HV wiring harnesses are never one-size-fits-all. Design flaws often originate in the early stages of the development cycle. Issues such as incorrect cable lengths, poor routing, or incompatible terminal crimps can prevent proper integration into the vehicle platform. Inaccuracies during the design or manufacturing phase can lead to misalignment, insufficient grounding, or reduced insulation performance under load.Work with experienced suppliers who use precision cutting and crimping equipment, adhere to strict quality standards, and understand the specific power and safety requirements of EV platforms. Simulation tools and 3D harness routing should also be employed to verify fitment, reduce EMI risks, and prevent mechanical interference.
2. Specify Fully Compatible HV Components
HV harnesses must be designed as complete, interoperable systems. Every component—from HV connectors and cables to shielding, sensors, and HVIL pins—must meet the voltage, current, and insulation resistance specifications of the EV application. For example, using a 70mm² cable in a 500A circuit while mismatching the connector’s rated current could result in overheating or premature failure.Modern EV platforms also demand shielding against EMI to avoid cross-talk between control signals and high-voltage lines. Mismatched shielding or grounding paths can degrade signal integrity and system reliability. Ensure compatibility between all mating parts and pay attention to interface standards such as IP67/IP6K9K ratings, dielectric strength, and mechanical keying.
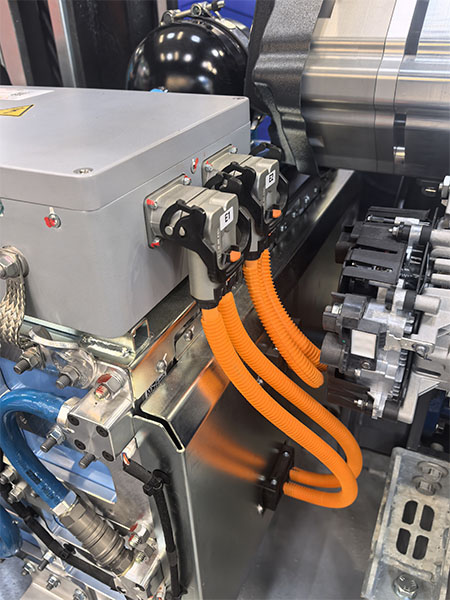
3. Select High-Quality Materials for Harsh Environments
Not all materials are created equal—especially in demanding automotive environments. HV cables and insulation materials must withstand exposure to high temperatures, chemicals, oils, moisture, and vibration over the lifetime of the vehicle. Cheaper copper alloys may seem cost-effective but are prone to fatigue and thermal instability, especially under repetitive load cycles.Instead, use automotive-grade, finely stranded copper conductors and XLPE or silicone-based insulation materials with excellent thermal and dielectric properties. Similarly, overmolded seals and grommets must maintain flexibility and integrity in extreme conditions to prevent water ingress, insulation breakdown, or connector corrosion.
4. Eliminate Crimping and Soldering Defects
Reliable electrical joints are critical in HV systems. Crimping is the most common method for terminating HV wires, but improper technique—due to tool wear, operator error, or incorrect die settings—can lead to poor conductivity, increased resistance, or failure under load.Automated crimp force monitoring, pull tests, and cross-sectional analysis should be standard quality checks. When soldering is required (especially for sensor wires or braided shields), technicians must follow precise thermal profiles to avoid cold joints or insulation damage. In EVs subject to vibration and thermal cycling, poor joints can become hot spots or trigger HVIL faults.
Work with trained personnel, calibrated tools, and documented assembly processes to maintain consistency and reduce variability.
Final Thoughts
Preventing high-voltage harness failures in electric vehicles requires a comprehensive approach—from robust design and material selection to proper assembly and testing. By collaborating with experienced harness manufacturers and specifying components tailored to EV environments, OEMs can ensure that their high-voltage systems deliver safe, reliable, and long-lasting performance.
Message
If you are interested in our products, please fill in the message form below. Our sales representative will contact you within 24 hours.