The Application of Ultrasonic Welding Technology in Electric Vehicle Industry
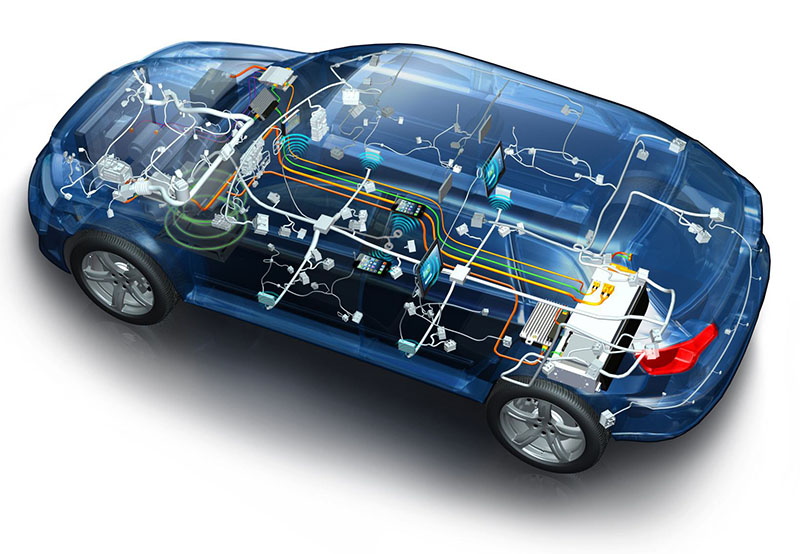
However, the growing demand for electric vehicles has brought many new challenges to the automotive industry, including: lightweight body structure, electrical and electronic components manufacturing, and battery manufacturing etc.. If EV manufacturers are to guarantee the highest quality levels and achieve the safety and environmental certifications associated with electric vehicles, innovative and economical production solutions are needed.
Ultrasonic welding technology is used and recognized by everyone because of its high efficiency, highly reliable connection and environmental friendliness. These characteristics are also in line with the requirements for electric vehicle production. Therefore, ultrasonic technology is an ideal process to solve many problems related to electric vehicle production.
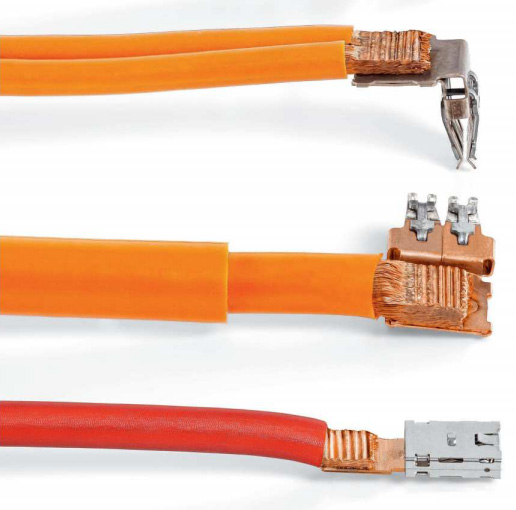
1. Reliable Connection of High-voltage Cables for Electric Vehicles
The motor used in electric vehicles must be able to provide full power output at the moment of starting. This requires reliable connection of high-voltage cables in the car. Cables and plugs connecting charging stations to high-voltage batteries require reliable, low contact resistance connections to enable fast charging. This usually requires effective welding of copper, aluminum, or a combination of the two to achieve the vehicle's high-voltage cable connections.Cables with cross-sections of 70mm², 95mm² or 120mm² must be firmly welded to the high-current connecting lug. Design engineers require the welding width to be as narrow as possible to save installation space. While it is difficult to achieve using traditional processes, it is now easy to achieve reliable connections using ultrasonic welding techniques.
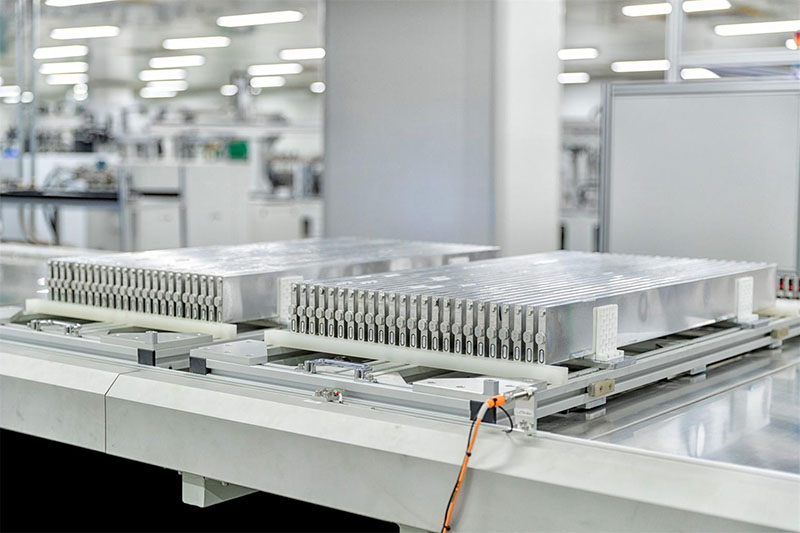
2. Ultrasonic Welding of Soft Pack Batteries Tabs
During the welding process of ultrasonic welding, no current flows through the weldment, and no arc is generated in the electric welding mode. Since ultrasonic welding does not have problems such as heat conduction and resistivity, it is undoubtedly an excellent choice for non-ferrous metal materials. The welding method also saves energy. Tesla has applied a specific application method of ultrasonic welding technology, WireBonding, in its battery system, making the application of ultrasonic welding technology in the field of power battery group connection more and more discussed. The application of ultrasonic welding in power batteries mainly focuses on tab welding and fuse welding.3. IGBT Power Semiconductor Ultrasonic Welding
Another ultrasonic welding process used to produce IGBT power semiconductors. An IGBT is a type of device that can switch current quickly with minimal losses and is a key electronic component in power converters used in electrical drives and battery charging systems. Ultrasonic waves are particularly suitable for welding IGBTs on sensitive ceramic substrates.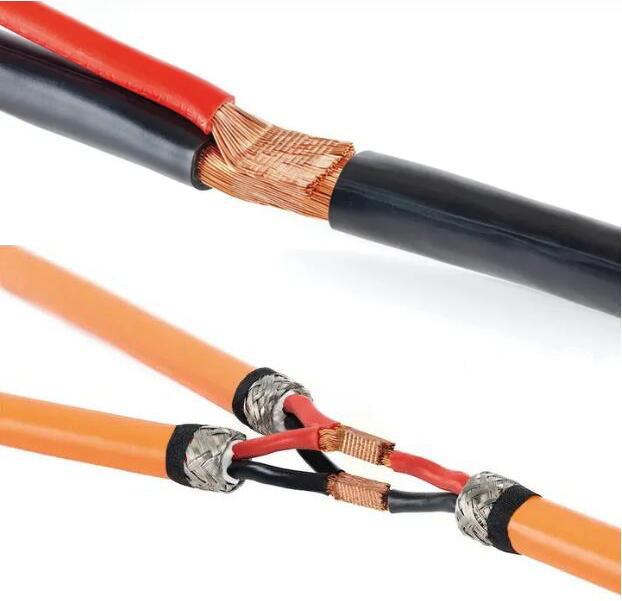
4. High Voltage Wire Harness Welding for Electrical Connections
Electric vehicles have fewer moving parts, which greatly reduces maintenance costs and improves reliability. Ultrasonic welding systems themselves are very reliable and low maintenance. Therefore, when reliable long-life electrical connections are required to meet the high quality standards required by the automotive industry, wire joining using ultrasonic processes is the preferred solution.The average automotive high-voltage wiring harness contains 180 ultrasonic welded joints, and this number increases with each passing year. OEMs are adding more electronic features to cars, which requires more connectors. The high voltage connectors and wire terminals form a long, complex, heavy-duty wiring harness that controls the entire vehicle electrical system. Due to the inherent labor intensity of wire processing, wire splicing has been a primary focus of wire harness manufacturing. However, the wire harness industry still uses crimping or resistance welding for applications such as small wire crimping or tin wire splicing.
Generally speaking, ultrasonic welding is not feasible for tinned parts or hard materials such as steel. This is where resistance welding or laser welding options become viable. However, when it comes to welding aluminum to another non-ferrous metal, ultrasonic welding is the ultimate choice. Due to its cold fusion welding properties, aluminum can be welded securely without melting or being significantly affected by heat. The benefits of ultrasonic welding apply to thermally conductive materials such as aluminum, copper and magnesium, which can be cumbersome to weld with resistance welders and lasers. Ultrasound is also very useful for joining thin and thick materials.
Ultrasonic wire harness welding has obvious economic and technical advantages: simple process, high cost-effectiveness; low contact resistance; high connection strength, etc. And the welding components are very flexible and easy to integrate into automated production lines. Even very thin cables with a 0.13mm2 cross-section and multi-strand cables used for high-speed data transmission can be welded using ultrasonic welding technology.
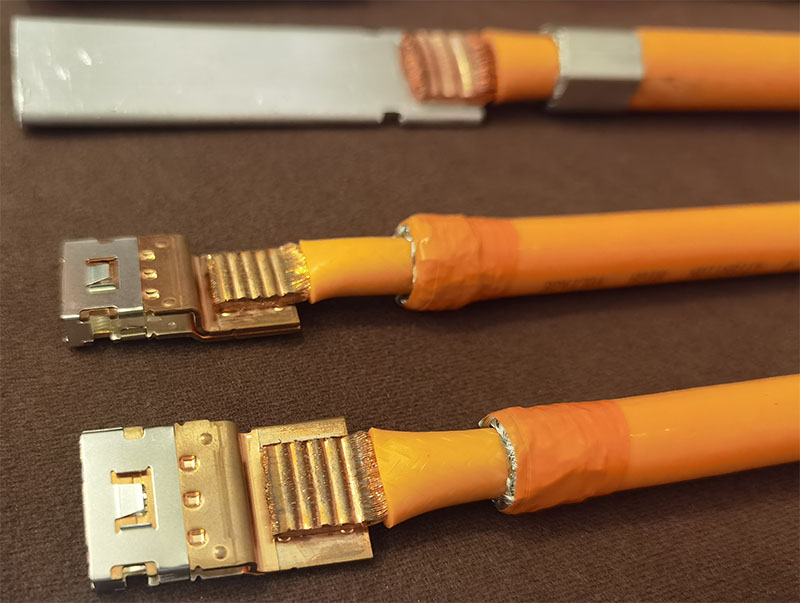
Advantages of High Power Ultrasonic Metal Welding
◆ A wide range of weldable materials can be used for the welding of the same metal materials, especially highly conductive and thermally conductive materials (such as gold, silver, copper, aluminum, etc.) and some refractory metals. It can also be used for the welding of dissimilar materials with widely different properties. Welding of metal materials (such as thermal conductivity, hardness, melting point, etc.) can also complete the welding of materials with widely different thicknesses and the welding of multi-layer foils;◆ Today’s electric vehicles are highly digitalized, and so are their production processes. The process parameters and welding result data of the ultrasonic welding system can be uploaded to the production management system via communication protocols to achieve production process monitoring and high automation, bringing a lot of added value to users.
◆ The weldment is not energized and does not require an external heating source. There are no defects such as microscopic pores in the joint, no brittle intermetallic compounds are generated, and no problems such as the splashing of molten metal that easily occurs during resistance welding occur;
◆ Lightweight structure: Lightweight means using more high-strength engineering plastics and composite materials instead of traditional metal. Thinner plastic bumpers, water-cooled valve bodies made of high-strength PA plastic, automotive radars encapsulated in PBT shells, through-type taillights, etc., all use ultrasonic welding processes in the production of these components. It can be said that ultrasonic technology has made a significant contribution to vehicle lightweighting. The welding process does not require adhesives and consumables, consumes less energy, and has no adverse impact on the environment.
◆ The physical and mechanical properties of the weld metal do not undergo microscopic changes. The static load strength and fatigue strength of the welded joint are higher than those of the resistance welded joint, and the stability is good;
◆ The oxide film or coating on the surface of the metal to be welded has little impact on the welding quality, and the surface preparation of the welded parts before welding is relatively simple;
◆ Welding requires less electric energy; the deformation of the weldment is small;
◆ No need to add any binder, filler or solvent. It has the advantages of simple operation, fast welding speed, high joint strength and high production efficiency.
Message
If you are interested in our products, please fill in the message form below. Our sales representative will contact you within 24 hours.